Shanghai University "JMST" review: Biomedical applications of 3D printing titanium alloys!
Source: Materials Science and Engineering
3D printing technology is a new precision forming technology and the core technology of the third Industrial revolution. The 3D printing technology of titanium and its alloys has received high attention in biomedical applications due to its potential for customized production, saving costs, time and resources, where the personalized customization of 3D printing can meet specific needs, enabling precise control of microstructure and structural design. In this paper, the latest development of bone substituting titanium-based biomaterials is reviewed from the aspects of materials, equipment, technology and technology. Secondly, topological design of cell structure, microstructure, mechanical properties and failure forms of titanium alloy after heat treatment, as well as in vivo and in vitro experiments on osteoblasts are discussed. Finally, the improvement methods of alloy defects are described. The application prospects of artificial intelligence, big data and machine learning in the field of 3D printing are also prospected.
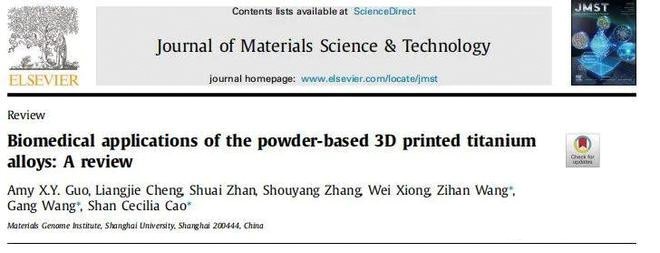
With an aging population and patients looking to maintain the same level of activity and quality of life, the use of orthopedic biomaterials has increased dramatically over the past few years. Driven by the huge demand for clinical orthopedic biomaterials, bone tissue engineering has developed rapidly, and a series of orthopedic biomaterials have been researched and designed. Iron and magnesium based biomaterials have been widely used with the help of 3D technology. Compared with iron and magnesium based biomaterials, titanium based biomaterials have high strength, low specific modulus and better biocompatibility, showing a unique competitive advantage in orthopedic biomaterials.
3D printed titanium-based biomaterials can be customized according to the different needs of individuals, not only can manufacture complex structures, but also has unparalleled advantages in cost, manufacturing cycle, personalized customization, etc., and can vigorously develop the application of this technology in orthopedics, dentistry, cardiovascular and other fields. However, the technology still faces many challenges, such as how to balance the relationship between porous bone growth and mechanical properties, the selection of additive manufacturing technology, and parameter optimization.
Researchers from Shanghai University summarized previous research work, pointed out the current challenges facing titanum-based biomaterials, and emphasized the important role of artificial intelligence in 3D printing parameter selection and structural optimization.
The relevant papers are entitled“Biomedical applications of the powder-based 3D printed titanium alloys: A review”发表在Journal of Materials Science & Technology。
Figure 1:
(A) Laser additive manufacturing
(B) Binder jet additive manufacturing
(C) Three multi-material extrusion additive manufacturing technologies
Figure 2:
Yield strength and plasticity of Ti6Al4V prepared by additive manufacturing and conventional methods
Figure 3
In vivo bone induction experiment of porous titanium and heat-sensitive collagen composite scaffold prepared by electron beam melting (EBM).
(B) Models in GBR that lead to cell response to Ti6Al4V-6Cu alloy;
Figure 4
Application of machine learning in 3D printing technology.
(A) Machine learning for biomedical 3D printing processes: from print to patient
(B) isotropic lattice structure design inspired by machine learning
(C) The contribution of metallurgy, mechanical modeling and machine learning to the specific processes of metal 3D printing.
Through the analysis and summary of 3D printing titanium alloy technology, the following conclusions are drawn:
(1) Different 3D printing technologies differ in terms of thermal scanning speed, power supply power, deposition rate, etc. Compared to traditional processes, the 3D printing preparation process has the typical characteristics of rapid heating and cooling, requiring precise control of process parameters to obtain high-quality and reliable parts.
(2) The topological structure of bone tissue is classified and described, and it is pointed out that one way to reduce the stiffness is to rationally optimize the topological structure of porous bone substitutes, so as to reduce the stiffness difference between bone substitutes and host bone, so as to alleviate the stress shielding problem.
(3) The influence of the characteristics of rapid heating and cooling on the microstructure evolution of titanium alloys was analyzed, and the mechanical properties could be improved by adjusting the two-phase composition and microstructure.
(4) The biocompatibility and bone-binding ability of porous titanium alloys after implantation were emphasized.
(5) Through the development of powerful digital tools, such as machine models and machine learning combined with metallurgical knowledge bases, 3D printed metals can be better developed.
It is pointed out that it is necessary to have a good grasp of process parameters and related factors affecting fatigue properties to develop effective identification and proof methods. For complex 3D printed geometry, such as porous and lattice structures, better testing and scanning methods, as well as non-destructive evaluation techniques, need to be developed. In addition, the continuous application of artificial intelligence and machine learning algorithms provides scientific guidance for the selection of machining parameters, which can improve the quality of parts and reduce the cost of trial and error. And machine learning can also gradually update process-microstructure-performance relationships based on experience. It is emphasized that we should vigorously develop 3D printing databases to lay the foundation for optimizing experimental design and accelerating personalized customization.