Information source: China Powder network
Ceramic additive manufacturing technology is an advanced manufacturing technology through the discrete material layer by layer manufacturing and superposition to obtain three-dimensional complex structure ceramic parts, with high material utilization, manufacturing flexibility, high degree of digitization advantages, suitable for small batch, complex structure of ceramic parts manufacturing. At present, the mainstream ceramic additive manufacturing technology includes laser selective sintering, stereoscopic light curing, ink direct writing and so on.
Additive Manufacturing (also known as 3D printing) and its predecessor, Rapid Prototyping, originated in the late 1980s. Its rapid development momentum and continuously explored application advantages make it become one of the hot topics in science, industry, economy and society in recent ten years.
The rapid development of additive manufacturing is inseparable from the expansion of applicable material systems and the optimization of finished component properties: polymer materials are the earliest developed and applied material systems, which are applicable to the most diverse types of additive manufacturing technologies, and the application fields also cover industrial and consumer markets. The additive manufacturing of metal materials started late but achieved fruitful results. All kinds of metals and alloys with more applications can now be manufactured by laser or electron beam melting, and related applications have been carried out in aerospace, human hard tissue repair and other fields. In contrast, although the additive manufacturing of ceramic materials started almost at the same time, it has not been realized until recent years with the launch of commercial light curing additive manufacturing equipment.
This milestone breakthrough quickly promoted ceramic additive manufacturing to become one of the hot spots in the academic research and industrial application exploration of ceramics in the world. The industry is looking forward to the advantages of ceramic additive manufacturing compared with traditional ceramic molding methods in terms of no mold, complex parts can be formed, and the economic community has also made optimistic estimates of the industry prospects in the field of ceramic additive manufacturing, and the output value of the related industry is expected to grow rapidly from less than $100 million in 2017 to $3.6 billion in 2028.
Ceramic additive manufacturing technology is an advanced manufacturing technology that produces three-dimensional complex structure ceramic parts by layer-by-layer manufacturing and superposition of discrete materials. It has the advantages of high material utilization rate, strong manufacturing flexibility and high digitization degree, and is suitable for small batch and complex structure ceramic parts manufacturing. At present, the mainstream ceramic additive manufacturing technology includes laser selective sintering, stereoscopic light curing, ink direct writing and so on.
Stereoscopic light curing (SLA)
Stereoscopic photocuring (SLA) is a manufacturing concept proposed by Swainson in 1977, and then Kodama really realized the process.
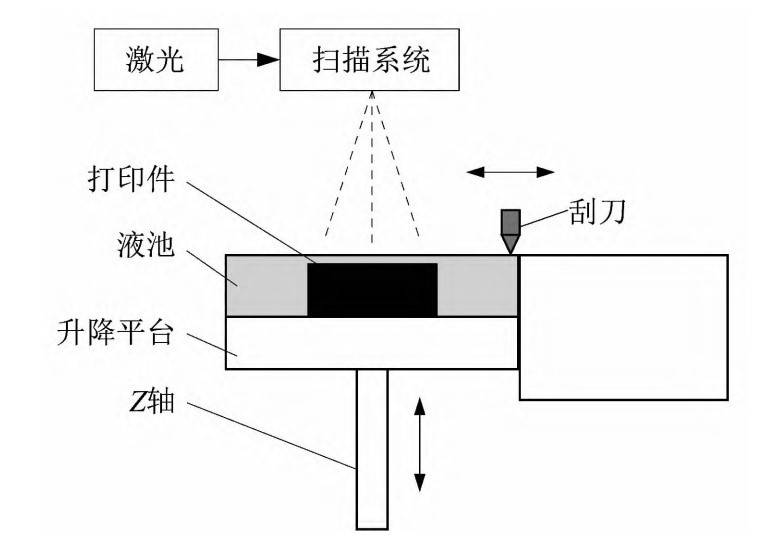
SLA schematic diagram (Source: Liu Panorama et al., "Application of Additive Manufacturing Technology in Ceramic Preparation")
The raw material of SLA process is mainly the ceramic resin mixed with liquid resin and ceramic powder. Compared with the traditional process, the ceramic samples prepared by SLA process not only continue the characteristics of good physical properties of ceramics, but also ensure the surface quality and dimensional accuracy of the products. However, there are also many constraints in using SLA technology to print ceramic bodies. When SLA technology is used to prepare ceramic bodies, different pastes need to correspond to different wavelengths of ultraviolet light, which puts higher requirements on the manufacturing environment and increases the manufacturing cost. In addition, the viscosity of the ceramic resin used in SLA technology should be less than 3Pa·s to ensure that the slurry has a certain fluidity, which makes the solid volume percentage of most ceramic resins less than 40%, resulting in the sample of these ceramic resins after degreasing sintering, most of them will appear drastic shrinkage and deformation, and even lead to the collapse of the entire ceramic body in serious cases. At present, the main method to solve this problem is to change the material in the ceramic resin.Melt Deposition Molding (FDM)Fused deposition molding (FDM) process was first proposed by American scholar Dr. Scott Crump in 1988, and is widely used in 3D additive manufacturing of organic polymer materials because of its easy implementation, fast printing speed and low cost. Usually used in FDM technology is mainly thermoplastic polymer materials, these polymers are made into linear raw materials, these wires through the nozzle of the FDM printer heating and melting, and is extruded from the nozzle, accompanied by the movement of the nozzle, layer on the base surface deposition to form the designed shape, and finally made of the required parts.Continuous fiber reinforced SiC prepared by FDM (Source: Wang Changshun et al., "Research and Application Progress of Additive Manufacturing Technology for SiC Ceramics")
With the development of material technology, more and more high polymer materials with good biocompatibility, low melting temperature and excellent mechanical properties have emerged, making FDM technology and ceramic system preparation opportunities. The results of this research are mainly used in biomedicine. Researchers by combining PLA, ABS and hydroxyapatite, using FDM technology to prepare artificial bone, and implant it into the patient's body, through the implant to stimulate bone growth, this technology helps the field of bone implantation out of the natural human bone shortage and xenogenic bone rejection dilemma.
Compared with other additive manufacturing methods, FDM technology has the advantages of low cost and no need for supporting materials in the preparation of human ceramic bones. At the same time, the study shows that the compressive strength of human bone is between 4 and 12MPa. By adjusting the porosity of these artificial bones, after degreasing process, the compressive strength can reach 16MPa, and the shrinkage rate is about 8%, which greatly ensures the geometric similarity between the actual sample and the design model. However, the initial ceramic prepared by FDM technology still needs to undergo degreasing sintering, which brings the problem of cracking and deformation. At present, the way to solve these problems is mainly through modifying the design of 3D model and improving the sintering method of ceramic green billet.
Selective Laser Sintering/Melting (SLS/SLM)The selective laser sintering (SLS) technique was first proposed by Carl Ckard in 1989, and its working principle is shown in the figure below. The powder in the powder storage bin is evenly laid in the powder bed by the roller, the powder is selectively sintered by the laser through the scanning system, and then the shaped piston is lowered, the roller re-lays the powder, and the required parts are formed by stacking layers.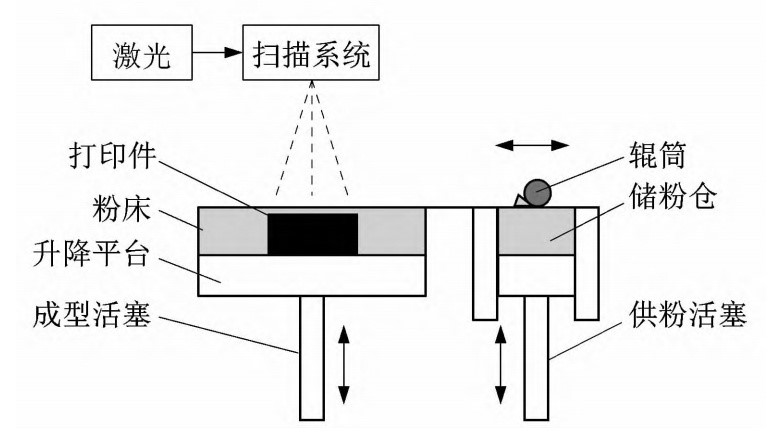
SLS/SLM schematic diagram (Source: Liu Panquan et al., "Application of Additive Manufacturing Technology in Ceramic Preparation")
SLS technology can be divided into two types when used in ceramic system preparation: additive and additive free. When the powder containing additives is heated by laser, the additives melt and bond the ceramic particles to form a whole, so as to obtain green parts; The solid powder without additives is generally mixed by two kinds of ceramic powder. When laser heating, the powder with low melting point is heated and melted, and the ceramic particles with high melting point are bonded. Compared with the manufacturing method containing additive powder, the low melting point powder acts as the role of melting and bonding the high melting point ceramic particles with the additive, and the advantage of this operation is that the degreasing step is eliminated. Different from SLS technology, selective laser melting (SLM) retains the characteristics of laser heating, but the technology does not need to add a binder, but through heating to melt all the powder and stick to each other, and then accumulate layers to obtain the ceramic body.
SLS/SLM technology has the characteristics of multiple application materials, low loss rate and simple process. Compared with other additive manufacturing methods, it has fast molding speed and high repeatability. However, there are two major problems that seriously limit the application of this process in industry: (1) In SLS technology, the removal of additives leaves pores, which reduces the mechanical properties of the formed parts; ② Low molding accuracy, high surface roughness.
Ink Direct Writing (DIW) Ink direct writing technology originated from the automatic grouting molding technology proposed by J.Cesarano et al., Sandia National Laboratory in the United States in 1998. At first, it mainly aimed at the three-dimensional model molding manufacturing of ceramics and other materials, and gradually developed into today's DIW additive manufacturing technology after continuous research and expansion in the later period.
Continuous fiber DIW forming equipment and process principle (Source: Wang Changshun et al., "Research and Application Progress of SiC Ceramic Additive Manufacturing Technology")
High viscosity liquid or solid-liquid mixture slurry is stored as ink material in the cylinder and connected to the nozzle. It is installed on a three-axis CNC platform that can complete three-dimensional movement under computer control. The ink material is continuously extruded from the nozzle by mechanical pressure or pneumatic pressure and preformed on the base. After the corresponding post-treatment (volatile solvent, heat curing, light curing, sintering, soaking, etc.) according to the material characteristics, the final three-dimensional molding component is obtained.
DIW additive manufacturing technology has the advantages of low equipment requirements, low manufacturing cost, wide application range of raw materials, high molding accuracy and flexible manufacturing. The disadvantage is that the ceramic prepared by DIW has poor accuracy and many defects, and it generally requires subsequent processing such as curing and sintering after direct writing. The accuracy of the final molding component depends not only on the formula of the ink material, the physicochemical properties of the components, the viscosity and rheological properties of the system, but also on the direct writing parameters (nozzle diameter, pressure size, platform moving speed, etc.).
Digital Light Processing Technology (DLP)Digital Light Processing (DLP) was first proposed by Larry Hornback in 1977 and commercialized by Texas Instruments 19 years later. The principle of DLP technology is similar to SLA technology. The specific difference between DLP and SLA technology is that DLP technology uses a wide band of projected light to project the cross-section image of the required sample on the surface of the photosensitive paste, and accumulates the sample layer by layer. The core component of DLP is the DLP chip, that is, the digital microscope equipment, which directly determines the geometry and printing accuracy of the sample.
DLP technology has the advantages of high precision and short time, and its application in ceramic body printing is mainly concentrated on small and complex structure products. When DLP technology is used in ceramic preparation, due to its low light intensity, the photoinitiator and free radical crosslinking polymerization reaction is poor, resulting in incomplete curing, which is usually solved by adding binder in the slurry. The ceramic paste with binder added was DLP 3D printed. The initial photocuring process made the sample have a certain conformal ability, and then it was heated in the oven to play the bonding role of the binder, so that the green geometry was fixed, and then the degreasing sintering step was carried out. However, many studies have shown that there are still problems of cracking, deformation and shrinkage of sintered samples. Therefore, like SLA technology, increasing the solid content of printing ceramic paste and suitable degreasing sintering method are still the research focus of DLP technology.
Conclusion and prospect
Compared with traditional ceramic preparation methods, additive manufacturing technology can realize the preparation of ceramic systems with more complex geometric structures, and meet the development needs of ceramic materials in various fields. The scientific research and application development of ceramic additive manufacturing will remain hot for quite a long time, and with the gradual solution of technical problems, the comprehensive performance of ceramic components of additive manufacturing will be further improved, first of all, gradually reach the manufacturing level similar to that of traditional manufacturing components. Then it will further realize the manufacturing of personalized functional ceramic parts through more refined and personalized structural regulation.
At the same time, we should also see that there are still many shortcomings in the ceramic body prepared by additive manufacturing technology, and there are still many obstacles in the widespread use of additive manufacturing technology in ceramic manufacturing. For example, the production time is long, the mechanical properties are lower than the traditional way of manufacturing ceramics, cracking shrinkage after processing; In addition, larger sizes (such as a few meters) of ceramic parts are still difficult to prepare with additive manufacturing techniques.
In summary, the future research of additive manufacturing technology in the field of ceramic system preparation should mainly focus on the development and post-processing of slurry, and it is also necessary to improve the molding technology to achieve the ceramic system preparation close to the design model in a relatively short time.
Reference materials:
1. Song Lu et al., "Additive Manufacturing" : To promote the design of personalized ceramic materials "molding - Quality integration" based on additive principle
2, Wang Changshun et al., "SiC Ceramic Additive Manufacturing Technology Research and application Progress"
3. Jiamin Wu, "The Emerging Ceramic Additive Manufacturing"
4, Liu Panorama et al., "Application of Additive Manufacturing Technology in Ceramic Preparation"
5, Jiang Yifan et al., "Ink Direct Writing Additive Manufacturing Technology and its Research Progress in the field of Energetic Materials"